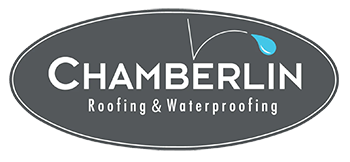
Chamberlin Roofing & Waterproofing
Using Vista, Hilti ON!Track™ and Vista Integration
Maintaining control over tools and equipment is a critical component of operational efficiency. Tools that are misplaced, lost, or not available when needed can lead to project delays, increased costs, and frustration. Through advances in technology, contractors like Chamberlin Roofing & Waterproofing are integrating tool tracking software with their construction ERP to mitigate these challenges, streamline operations and boost productivity.
For over a century, Chamberlin has provided personalized, professional roofing and waterproofing for the entire building envelope. Over the years, the company expanded beyond its Texas headquarters to offer services in Oklahoma, Louisiana and Arkansas. Technology has been foundational to Chamberlin’s success, driving efficient and profitable delivery of a wide range of services that continue to grow in scope.
Disconnected Systems Lead to Siloed Data
As Chamberlin expanded and its number of assets increased, tracking and managing tools and making that information visible to teams across the company became critical to its success.
In 2014, Chamberlin began using Trimble’s construction ERP, Viewpoint Vista, as part of Trimble Construction One, a connected stack of Trimble solutions that brings together the company’s people, data, and workflows in a shared data environment. The company also implemented a standalone tool tracking software to help better track and manage its assets across employees, projects and locations.
While the tool tracking software was living up to its promise, Chamberlin began to feel the pains of working with a solution that siloed data. The lack of integration between its tool tracking software and Vista led to redundant data entry and manual reconciliation, making information difficult to track down. For Chamberlin, this translated to wasted time and resources that could otherwise be spent on productive tasks. “Employees were spending hours manually entering data to ensure it was reflected in both systems, which was time-consuming and caused delays,” said Daniel Rufrano, controller at Chamberlin. “Warehouse managers assigning a tool to a new hire had to track down the employee’s information because it wasn’t yet available in the tool tracking software. Our warehouse managers had to bounce between multiple systems to track down employee information. This same delay made it difficult to reclaim our tools when an employee was terminated.”
The tool tracking software lacked the capability to track consumables. “These items were tracked using pen and paper,” said Rufrano. “The process involved a lot of administrative work. Someone in the office would typically input tool usage information from a piece of paper into a spreadsheet so they could upload it to Vista. This process made billing for consumables lengthy and difficult.”
Automating Tool Tracking from the Field to the Office
When Rufrano heard about a new integration between Viewpoint Vista and Hilti ON!Track, he was intrigued. “We were happy with our current tool tracking software, but I knew we would get a lot of added value from bringing tool tracking data into Vista,” he said. “We did a little research and discovered this integration would be a huge win for us.”
Chamberlin adopted Hilti ON!Track and began integrating it with Viewpoint Vista.
It wasn’t long before the benefits of streamlined workflows and seamless data integration translated to time savings, efficiency gains and more accurate invoicing. Chamberlin now has a single source of truth that gives office and field teams visibility into tool usage. This has been especially helpful when onboarding and assigning tools to employees.
“When new employees are onboarded in Vista, their information is automatically visible in ON!Track,” Rufrano said. “Our warehouse managers do all of their work in ON!Track without needing to hunt for information or cross-reference with Vista. The integration has eliminated manual processes and given warehouse managers instant access to the information they need to assign tools to new employees without delay. It’s also helped us reclaim tools when an employee is terminated. Before, an employee would wrap up work and be long gone before the warehouse manager knew they were terminated. Visibility into an employee’s status has allowed us to get tools back before they disappear.”
Today, it takes seconds for warehouse managers to find tools and transfer them to an employee, jobsite or back to the warehouse. “With so many employees coming and going, it’s important to know who has a tool, when it was last checked out and whether or not it needs to be serviced,” said Rufrano. “This visibility across the field, warehouse and office has been a big win for us.”
Automated and Allocated Tool Utilization
Hilti ON!Track calculates tool utilization and syncs with Viewpoint Vista, automatically applying the usage to the right job so teams in the office can accurately invoice for equipment and tool usage. Employees in the field use the mobile ON!Track app and scan a QR code on the tool. The information is captured and synchronized to Vista, giving accounting teams the utilization data they need to run automated, rule-based invoices for each job. “We’re able to accurately invoice customers without delay, so rather than losing money on unbilled usage, we’re generating revenue from our assets.”
Synchronized Data
The integration eliminated the need for warehouse managers to keep paper lists and for teams in the office to transfer those lists to spreadsheets before importing them into Vista.
“The integration removed the need for a full process on the administrative side,” said Rufrano. “Before, information from the field had to be transferred to a spreadsheet and then uploaded to Vista. This took considerable time and increased the potential for errors as information moved from one format and system to the next. It took too long to populate both systems, so not only could we make good use of the data, but our teams in the office also wasted a lot of time that could be better spent on more important tasks.”
“Now, no one keys in information. The tool usage is tracked in ON!Track and automatically visible in Vista. Our accounting team looks it up and sends the invoice. It’s saved us at least 20 hours a month and is miles ahead of what we had before.”
Looking Ahead
Tools are one of a contractor’s most valuable assets. Inefficient tool management slows down work and impacts the bottom line. Research shows that jobsites lose one day per month of productivity on average searching for tools. That productivity loss is also evident in the time accounting teams and warehouse managers spend manually entering and tracking down information. The Hilti ON!Track and Vista integration maximizes the benefits of asset/tool tracking data by automatically providing the information needed to track, allocate, bill and estimate for accurate tool and equipment use.
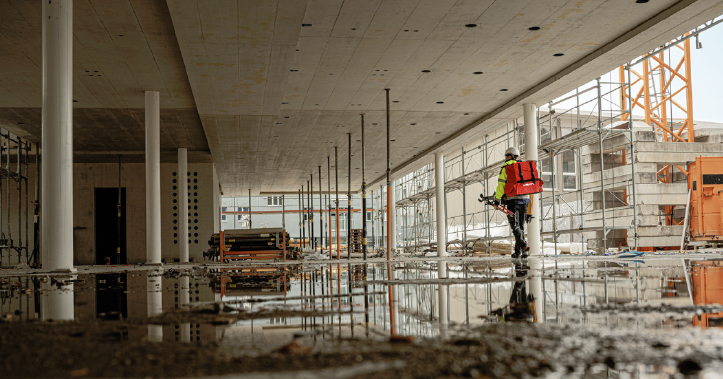
Learn more about how companies like Chamberlin are automating tool tracking and utilization to increase productivity, improve asset visibility, ensure accurate invoicing and more.
About Trimble
Trimble is developing technology, software and services that drive the digital transformation of construction with solutions that span the entire architecture, engineering and construction (AEC) industry. Empowering teams across the construction lifecycle, Trimble’s innovative approach improves coordination and collaboration between stakeholders, teams, phases and processes. Trimble’s Connected Construction strategy gives users control of their operations with best-in-class solutions and a common data environment. By automating work and transforming workflows, Trimble is enabling construction professionals to improve productivity, quality, transparency, safety, sustainability and deliver each project with confidence. For more information, visit: construction.trimble.com