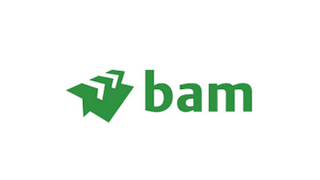
BAM Construction
Building an extension to Great Ormond Street Childrens’ Hospital in London required a fast and effective monitoring solution to ensure that key construction milestones were met on time.
The 30,000 square metre Mittal Children’s Medical Centre expansion project represents the second phase of a major £321m redevelopment programme at the famous children’s hospital, located near Holborn in central London.
Intended to increase the facility’s overall capacity by 20%, the project will see two ultra energyefficient clinical buildings built to house facilities for pioneering new patient treatments, clinical research and medical training.
The first block — the £90m Morgan Stanley Clinical Building, designed by Llewelyn Davies Yeang architects — is currently on site and due for completion at the end of the year. Spread over eight storeys, it will include a new cardiac unit, theatres, plus renal and neurological units, and will be serviced by a range of hi-tech green technologies including combined cooling, heating and power units (designed to achieve a 60% reduction in carbon emissions), sensor taps, water-efficient toilets and showers and natural daylight detectors.
Viewpoint Construction Software’s Field View, formerly Priority 1 construction project information management system is being used by main contractor BAM Construct to monitor various aspects of construction delivery, as construction manager Richard Pateman explains: “We previously used Field View as a snagging tool, but at Great Ormond Street we wanted to use it as a progressing tool to monitor construction work in individual areas, which was a major concern,” he said. “Processes in hospital buildings are very complicated and require numerous inspections by our managers. For example, there is more emphasis on inspections prior to wall and ceiling closures etc. and because the building is divided into 700 individual areas, monitoring progress required a tool that would allow us to perform checks and analyse progress quickly without the need for time-consuming paperwork.”
Field View improves efficiency by making construction site paperwork easily accessible via a mobile computer (PDA). At Great Ormond Street, BAM put together a schedule to identify key completion elements of the construction programme. Each week, site managers, armed with PDAs, then inspected work on site and noted down, via dropdown checklists on the PDA, whether those elements were completed, underway or not yet started.
With that information, the team could then monitor overall construction progress on an area by area, or even room by room, basis, says Pateman: “The checklists picked up the most important phases of construction and included up to 150 items, depending on complexity of each room. After managers completed weekly checks with the PDAs – there are four devices in total - we are able to produce a bar chart to visually see the progress of each individual room and of entire floors. It allowed us to identify whether there’s a problem in the work process and go back and investigate why it occurred,” he adds.
BAM’s younger managers took to the new technology straight away, and despite some teething problems, the older managers soon found the software simple to operate, says Pateman: “We tried to make progress monitoring as simple as possible, the drop-down check lists are easy to select - you simply tap the screen with a pointer - and the traffic light system of green, red or amber gives a clear visual clue as to the progress of each item.”
Using Field View has cut the amount of paperwork BAM needs to process on site, freeing up managers’ time to focus on more project-critical jobs, says Pateman: “You simply update and clear items on the PDA, and the information is transferred to a PC when the PDA is synced with it, so there’s less paperwork involved, managers don’t have to spend their time inputting paper notes onto a PC database, and you have all the information in the same place instead of scattered over various documents,” he says.
With just eight weeks until project completion, BAM has moved on from using Field View for construction delivery monitoring to snagging operations and there are plans to expand its remit in future. “Field View is capable of far more than we used it for and we are seriously considering expanding the packages we apply it to or monitoring new activities, such as safety or other processes. In some instances, the greater efficiency enabled by Field View may mean we require less site admin staff,” concludes Pateman.