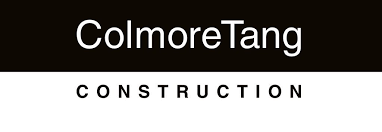
Field View Increases Colmore Tang’s Project Visibility
Using Viewpoint Field View
Colmore Tang Construction was originally launched in 2013 and is now recognized as one of the fastest-growing contractors in the UK. In 2017, the company won ‘Best Main Contractor to Work With (Under 50M)’ at the Construction Enquirer Awards, and since then revenue has continued to grow. Colmore Tang has delivered more than 2,000 residential units since 2014 and prides itself on its breadth of diverse projects across the country.
Colmore Tang Living provides a bespoke service to housing associations and providers of social housing. With the increased demand on new build housing projects Colmore Tang Living needed a field solution that allowed its workforce to spend more time on site. This case study features the St Martin’s Place project, which included the development of 228 apartments in which Colmore Tang utilized off-site construction techniques with the manufacture of concrete panels in Belfast.
Before
- Too much time spent doing paperwork in the office
- Poor communication
- Health and safety data wasn’t being recorded effectively
- No overview of project performance
- Poor collaboration with supply chain
After
- Improved visibility of project performance
- Increased productivity
- Greater control over projects
- Improved defect management
- Improved compliance with health and safety measures
Challenge
Colmore Tang faced the challenge of ensuring it had the correct systems in place to cope with rapid growth of the business and increased demand for social housing. The company recognized workers were spending too much time in the office filling out paperwork when time could have been better spent on site. Without a common data environment (CDE) in place, Colmore Tang didn’t have a system that allowed the communication of project updates and it didn’t have a central view of what parts of the project were performing and which parts weren’t. Colmore Tang’s management team also wanted to improve their workers’ health and safety of their projects, as well as reduce the number of defects found — both of which were proving difficult with paper-based systems.
A modern solution was needed that enabled site workers to spend more time on site, improve defect management, monitor health and safety and monitor construction compliance while being able to record all of this effectively.
Solution
Colmore Tang selected Viewpoint Field View™ to replace manual processes and improve project management with a powerful, yet easy-to-use digital solution. Field View is a cloud-based and off-line mobile solution that streamlines field tasks and automates workflows for quality assurance and control, safety, project delivery and handover.
Field View Replaces Pen and Paper
With Field View, users can create custom and pre-configured health and safety forms to capture and transmit data from field-to-office in real time. As well as digitizing on site forms, Field View also replaces pen and paper in the field when it comes to snagging. Field View allows users to take photos and record snags in real-time and send directly to clients and/or the back office, improving the management and monitoring of tasks and client collaboration. Field View allows customers to have one central view of the status of all tasks within a project, hence why project management and efficiency of closing out tasks is instantly improved.
Field View is used by Colmore Tang for everything from monitoring health and safety items to reducing defects on site as well as gaining insight into project performance to better guide decision making.
Results
Beyond a simple snagging tool, Colmore Tang saw immediate benefits in business operations by implementing the product as a management solution that improves processes and communications. This gave the company better control over its projects and overall business decisions.
“All the information is automatically distributed to all parties concerned and it provides a golden thread of information, through from design to project completion,” said Nicola Markall, Colmore Tang’s construction compliance manager. “It’s an excellent project management tool. It allows us to see at a glance what projects are performing, what projects aren’t performing, why they’re not performing and where we need to focus more time and resource.”
Spend More Time on Site
Colmore Tang saw many benefits from changing from paper based systems to digital methods. Field View meant workers could spend more time on site rather than filling in paperwork at the office. “When people are out on site, we are able to build a safer job with fewer incidents and accidents that’s defect free and reaches a higher standard for our client,” Markall said.
The St Martin’s Place project was unique as Field View was used across the project in different locations. Colmore Tang was utilizing off-site construction techniques with the manufacture of concrete panels in Belfast by subcontractor Creagh Concrete. Structures were shipped to site as a finished unit, with windows and insulation already fitted.
Referring to this process, Stuart Millichamp, senior project manager for Colmore Tang said, “we use Field View to track the full process going through the full life-cycle of the product, from the moment it is manufactured to when it arrives on-site and then installed as a finished unit.” The collaborative nature of the product was vital for Colmore Tang and it resulted in freeing up time between contractor and subcontractor, with a comprehensive, trackable audit trail.
The real-time information Field View provides allowed Colmore Tang to manage the process of tasks moving through various stages of completion. The collaborative nature of the product ensured work from subcontractors could start at the right time and nobody was tripping over themselves.
“We run an open system so that sub-contractors can see where other sub-contractors are. That comes with risks in the sense that everything’s transparent, but what it does is it promotes the spirit of collaboration between the subcontractors so they know who is holding things up and who is getting ahead and we have to keep that rigidly enforced in order for people to make money,” said Steve Underwood, Colemore Tang’s chief operating officer.
Underwood stressed the importance Field View had in improving supply chain relations by moving towards an open system. The open system created “a process to enable them to plan and organize their works, they become more efficient, they make more money and they come to our sites and not somebody else’s.”