Quality Control vs. Quality Assurance in Construction
0%
There are lots of moving parts in the world of construction quality management. All construction teams must make sure a project gets completed to the highest standard and with minimal disruption.
Although differing in meaning, quality assurance and quality control often get used in similar contexts. They are dependent on each other and if quality assurance is the perspective, then quality control is the approach.
As you know, the construction industry loves an acronym. Do you know your QAs from your QCs, what the difference is between the two, and when is appropriate to use either? We’ll tackle all of your burning questions to make sure you’re nailing quality in construction.
What is quality assurance (QA) in construction?
Put simply, quality assurance is a predetermined set of activities that help to make sure a project is completed without any defects or issues. It’s a term used to describe lots of different elements that are used in a project to proactively assess, prevent defects, and mitigate risks.
For new projects, a project quality plan (PQP) will be created for each to help identify risks specific to the project, rather than using a more general set of quality assurance policies that might be in place. Each can – and should – vary by project, but as a minimum a PQP will usually outline the standards, requirements, specifications, and procedures. Some examples of what could be included in a PQP are:
• Establishment of objectives and performance indicators
• Creation of quality standards, procedures, and guidelines
• Reenforce company quality requirements (i.e. ISO 9001) and how this affects data collection
• Set out training and up-skilling requirements
• List out digital tools to be used on the project
• Evaluation of project requirements
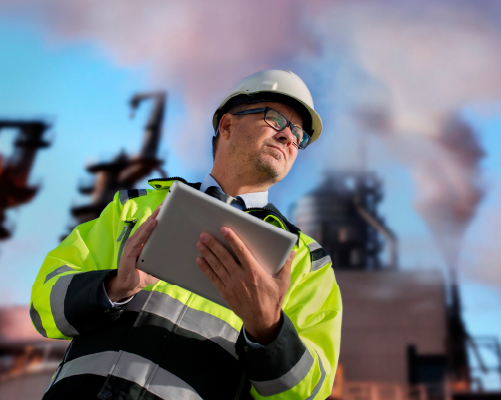
What is quality control (QC) in construction?
More broadly, quality control is also used to describe destructive and stress tests on materials to be used on a construction site. However, in the context of a construction project, quality control takes place after an action has taken place. It usually takes the form of inspections, tests, or evaluations.
One of the most common would be site inspections, undertaken by external inspectors or qualified managers armed with an inspection checklist or form. Inspections often look across building control, snagging, and health & safety as the 3 key areas.
Quality control processes forms an essential part of any quality management system.
Why is quality assurance so important?
Quality assurance is important in the construction process as it puts together a means tested prediction of what could happen, what might happen, and what can’t happen throughout the project.
Projects with robust quality assurance will likely have enhanced safety measures on site. This is because there will be a framework for mitigating risk, through the use of regular and thorough inspections, and clear procedures of how to handle risks should they appear.
Having discussions with various stakeholders to determine these factors helps hugely with cost saving through a project’s life cycle. If you’ve prepared for the eventualities and put steps in place to prevent them to the best of your ability, there’s no way it couldn’t save costs.
Naturally, this will lead to more efficient project management. The double-pronged approach of predicting any blockers and being able to quickly resolve any unexpected blockers that come up means that there’ll be less down time. It may be a few minutes here and there, but over a 6, 9, 12-month project, these minutes start to add up to big time savings that have been reinvested back into the project.
The key to creating good quality control procedures is consistency and continual improvement. To begin with, it’s likely that processes are clunkier than expected as teams begin to get used to new ways of working. Taking stock at the end of each project to see where things went well, where there were hold ups, and if there are any quality trends that need to be addressed.
What are the risks of not having a good quality management system?
It's not just a matter of a few lost pennies or staying back an extra couple of minutes at the end of the day. By now, you’ve probably gathered that the risks are great.
Additional Costs
The most obvious risk is unforeseen additional costs because work has to be redone and repaired. Project delays because of quality issues can cause prices to escalate, as well as cause a knock-on effect to other jobs, taking valuable resources away from those projects. Construction is already a tight margins industry, having good quality assurance in place can help protect profits.
Unsafe Working Conditions
Another risk is the potential for serious injury on site. Not having proper precautions in place that are regularly reinforced with inspections and spot checks can cause serious repercussions for the workforce. Life safety is key. There’s no excuse to put workers at unnecessary risk in an already high risk industry such as construction.
As well as the human consequences, the financial and legal repercussions for failing to put effective safety measures in place could also be devastating.
Damage to Reputation
It goes without saying, but failing to have good quality management processes in place can cause irreparable damage to your company’s reputation.
For main contractors, clients will soon begin to look towards those who can provide audit trails of information to put their money where their mouth is. For subcontractors with poor quality control, the ability to bid and win on future jobs will become more difficult once their bad reputation precedes them. The customer expects – and deserves – a quality build, so companies that can deliver a high quality final product will become the ones that fall into favour.
One thing’s for sure, when it comes to quality assurance, investing in people, process, and technology will alway pay dividends in the long run.